Hybrid Cloud and Integrated Intelligence of Smart Manufacturing Factories: The Role of Cloud Computing and Artificial Intelligence in the UAE
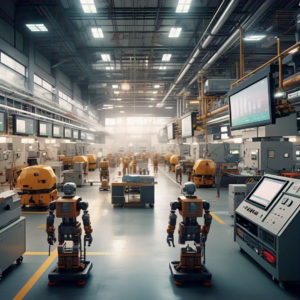
The evolution of manufacturing has reached a pivotal point with the rise of Industry 4.0, emphasizing the integration of advanced technologies like cloud computing and artificial intelligence (AI) to create smart manufacturing factories. This transformation enhances automation, flexibility, and efficiency in manufacturing processes. In this blog, we will explore the integrated intelligence of smart manufacturing factories, focusing on their architecture, operational mechanisms, and the technologies that facilitate this integration, particularly in the context of the UAE, by following Hybrid Cloud Best Practices: Seamless Integration and Security to ensure effective and secure implementation.
1. Architecture of Smart Manufacturing Factories: Leveraging Hybrid Cloud and Advanced Technologies
The architecture of a smart manufacturing factory is built upon three key pillars: horizontal integration, vertical integration, and end-to-end digital integration.
1.1 Horizontal Integration
Horizontal integration involves collaboration between various organizations within a value network. This integration allows seamless information, material, and financial flow among stakeholders, fostering an ecosystem that can quickly respond to market demands. In this context, smart factories can use shared resources and capabilities through hybrid cloud, leading to new business models and value networks.
1.2 Vertical Integration
Vertical integration focuses on the internal systems of a manufacturing facility, often leveraging hybrid cloud to connect subsystems like sensors, actuators, and enterprise resource planning (ERP) systems, creating a cohesive and flexible manufacturing environment. This integration enables real-time data collection and analysis, allowing dynamic adjustments to production lines based on changing product requirements. Smart machines within this framework form a self-organizing system that adapts operations based on real-time data inputs, enhancing overall efficiency and responsiveness.
1.3 End-to-End Digital Integration
End-to-end digital integration covers the entire value chain, from product design to delivery, often enhanced by hybrid cloud solutions. This integration ensures that all production stages are interconnected and can communicate effectively. By utilizing digital twins and simulation technologies, manufacturers can optimize processes, predict outcomes, and enhance product customization, resulting in a more agile manufacturing environment that can respond rapidly to customer needs.
2. Operational Mechanisms of Smart Manufacturing Factories
The operational mechanisms of smart manufacturing factories are driven by advanced technologies that enable communication, data analysis, and decision-making.
2.1 Internet of Things (IoT)
The IoT plays a crucial role in smart manufacturing by connecting machines, devices, and systems. Through sensors and communication technologies, IoT enables real-time monitoring of equipment performance, production processes, and environmental conditions. This connectivity allows for predictive maintenance, reducing downtime and improving overall efficiency.
2.2 Artificial Intelligence (AI)
AI technologies, including machine learning (ML) and deep learning (DL), are integral to the functioning of smart factories. AI algorithms analyze vast amounts of data generated by IoT devices, enabling manufacturers to gain insights into production trends, quality control, and resource allocation. For instance, AI can optimize production schedules based on historical data and real-time inputs, ensuring efficient resource utilization.
2.3 Cloud Computing
Cloud computing provides the necessary infrastructure for data storage, processing, and analysis in smart manufacturing. By leveraging cloud services, manufacturers can access scalable computing resources that facilitate complex data analytics and machine learning tasks. This capability is particularly beneficial for managing the massive volumes of data generated in smart factories, allowing for informed decision-making.
2.4 Edge Computing
Edge computing complements cloud computing by processing data closer to the source, reducing latency and bandwidth usage. In smart manufacturing, edge devices can perform real-time analytics and decision-making, enabling faster responses to changing conditions on the factory floor. This is particularly important for time-sensitive tasks, such as quality control and equipment monitoring.
3. Key Technologies in Smart Manufacturing: Exploring Hybrid Cloud and Advanced Innovations
Several key technologies underpin the integrated intelligence of smart manufacturing factories, enhancing their capabilities and operational efficiency.
3.1 Multi-Agent Systems (MAS)
Multi-agent systems (MAS) consist of autonomous agents that can communicate and collaborate to achieve common goals. In smart manufacturing, MAS, often supported by hybrid cloud technologies, can dynamically reconfigure production resources based on real-time demands. These agents negotiate resource allocation and scheduling, ensuring flexible and efficient production processes that adapt quickly to changing market needs.
3.2 Big Data Analytics
Integrating big data analytics into smart manufacturing, powered by hybrid cloud solutions, allows for extracting valuable insights from large datasets. By analyzing data from various sources, manufacturers can identify patterns, predict equipment failures, and optimize production processes. This data-driven approach enhances decision-making and improves overall operational efficiency, enabling faster responses to market changes.
3.3 Cyber-Physical Systems (CPS)
Cyber-physical systems (CPS) integrate physical processes with computational elements, often utilizing hybrid cloud solutions for real-time monitoring and control. In smart factories, CPS facilitate seamless interaction between machines, humans, and information systems. This integration enhances the responsiveness of manufacturing processes, improving overall system performance and enabling more agile operations.
3.4 Digital Twins
Digital twins are virtual representations of physical assets, processes, or systems, often supported by hybrid cloud technology. In smart manufacturing, digital twins allow manufacturers to simulate and analyze production processes, enabling predictive maintenance and process optimization. By continuously updating the digital twin with real-time data, manufacturers gain insights into performance and identify areas for improvement, enhancing overall operational efficiency.
4. Benefits of Integrated Intelligence in Smart Manufacturing
Integrating advanced technologies in smart manufacturing factories offers numerous benefits, including:
4.1 Enhanced Flexibility
Smart factories can quickly adapt to changing market demands and customer preferences. The ability to reconfigure production lines and resources in real-time enables manufacturers to produce customized products efficiently.
4.2 Improved Efficiency
By leveraging AI and big data analytics, manufacturers can optimize production processes, reduce waste, and improve resource utilization. This leads to increased operational efficiency and lower production costs.
4.3 Predictive Maintenance
The use of IoT sensors and AI algorithms allows manufacturers to monitor equipment health in real-time. Predictive maintenance strategies can identify potential failures before they occur, reducing downtime and maintenance costs.
4.4 Better Quality Control
Smart manufacturing technologies enable real-time monitoring of product quality, allowing manufacturers to detect defects early in the production process. This proactive approach to quality control leads to higher product quality and greater customer satisfaction.
4.5 Data-Driven Decision Making
Integrating big data analytics provides manufacturers with valuable insights into production trends, customer preferences, and market dynamics. This data-driven approach enhances decision-making and enables manufacturers to respond quickly to changing conditions.
5. Challenges and Future Directions
Despite the numerous benefits, implementing integrated intelligence in smart manufacturing factories also presents challenges:
5.1 Data Security and Privacy
The increased connectivity of devices and systems raises concerns about data security and privacy. Manufacturers must implement robust cybersecurity measures to protect sensitive information from potential threats.
5.2 Integration of Legacy Systems
Many manufacturing facilities still rely on legacy systems that may not be compatible with modern technologies, including hybrid cloud solutions. Integrating these systems into a smart manufacturing framework can be complex and costly, requiring careful planning and investment to ensure smooth interoperability and enhance overall efficiency.
5.3 Skills Gap
The transition to smart manufacturing requires a workforce with advanced technical skills, particularly in hybrid cloud and other emerging technologies. Manufacturers must invest in training and development programs to equip employees with the necessary skills to operate and maintain new technologies, ensuring a smooth shift toward more efficient and responsive production processes.
5.4 Standardization
The lack of standardized protocols and frameworks for smart manufacturing, particularly in hybrid cloud environments, can hinder interoperability between different systems and devices. Industry-wide standards are needed to facilitate seamless integration and communication, ensuring that diverse technologies and platforms work together efficiently in smart manufacturing.
Conclusion
The integrated intelligence of smart manufacturing factories represents a significant leap forward in the evolution of manufacturing. By harnessing the power of hybrid cloud, artificial intelligence, and other advanced technologies, manufacturers can create flexible, efficient, and responsive production environments. As the industry continues to evolve, addressing the challenges associated with this transformation will be crucial for realizing the full potential of smart manufacturing. The future of manufacturing in the UAE lies in leveraging integrated intelligence to meet the demands of an ever-changing market landscape. This exploration of integrated intelligence in smart manufacturing highlights the transformative potential of these technologies, particularly Hybrid Cloud Best Practices: Seamless Integration and Security, paving the way for a new era of manufacturing that is more connected, efficient, and responsive to customer needs.
If you are looking for software services, visit Cloudastra Technologies. Do you like to read more educational content? Read our blogs at Cloudastra Technologies or contact us for business enquiry at Cloudastra Contact Us.